Chemico applies a holistic, integrated approach to Chemical Lifecycle Management to provide programs that drive Sustainability across the enterprise. Our approach links Environmental, Social, and Economic factors both individually and collectively.
Chemico places significant emphasis on Sustainability, both internally and in support of our customers’ operations as well. This is reflected in our mission statement: “to add value to our customers’ supply chain, and value to our employees’ lives, and create positive impact in the communities in which we operate.” For more information, please see our 2023 Chemico Sustainability Report.Â
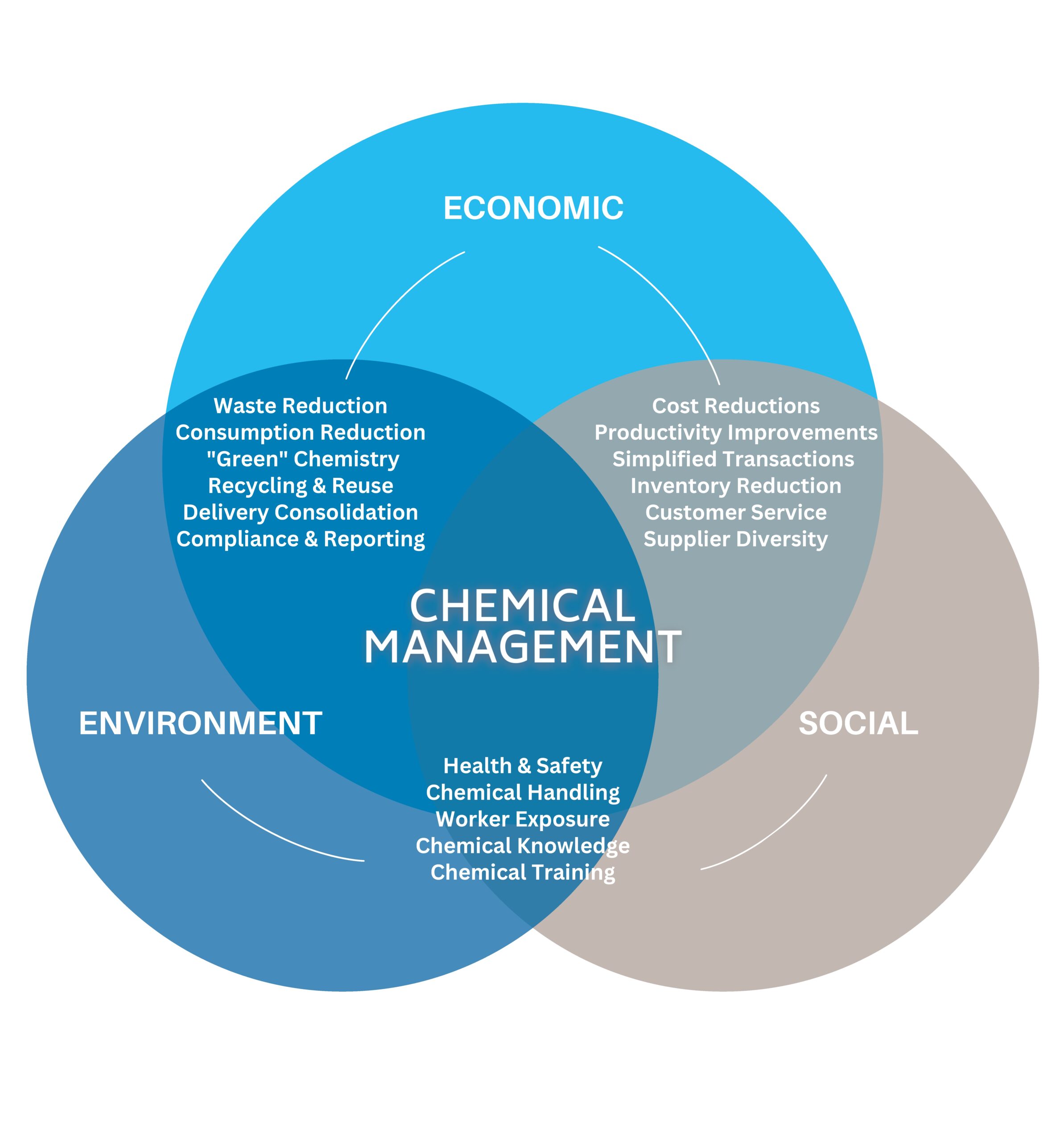