Chemico was hired to develop a chemical lifecycle management program for an aerospace components manufacturer to improve their quality compliance program, inventory control, and an overall reduction in waste and cost. The site included a wide variety of operations including metalworking, painting, electronics, assembly, and testing with multiple departments creating challenges in control and communication. Chemico, program supported the customer through a broad scope of work:
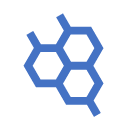
Integrated Chemical Management
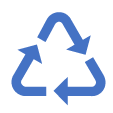
Waste and Environmental Management
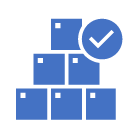
Inventory Management
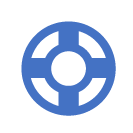
Shelf Life Management
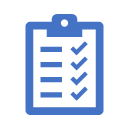
Quality Inspection
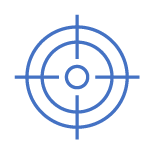
POU Management
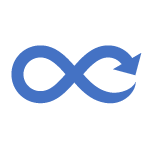
Technical Process Expertise
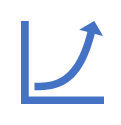
Productivity Improvements
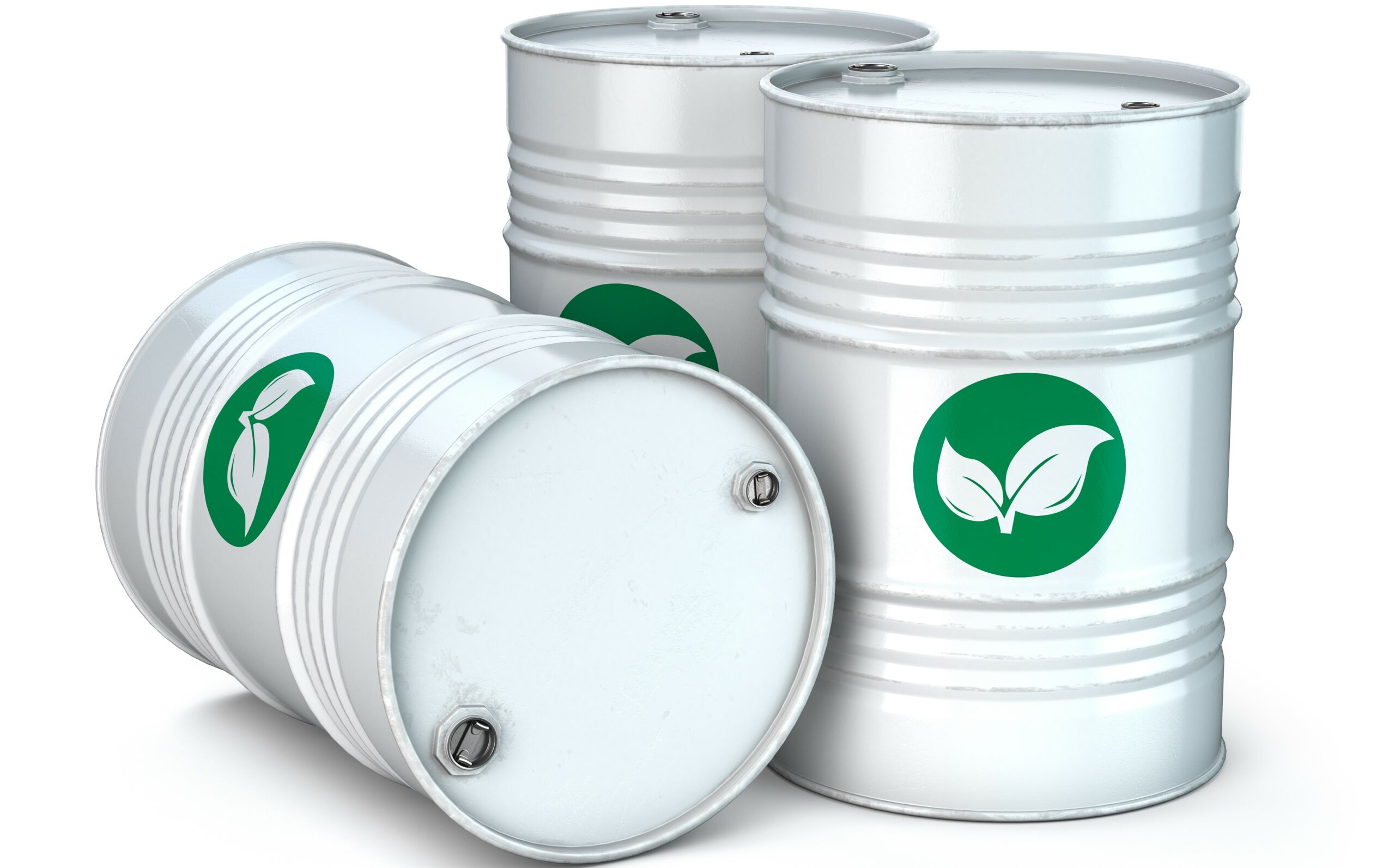
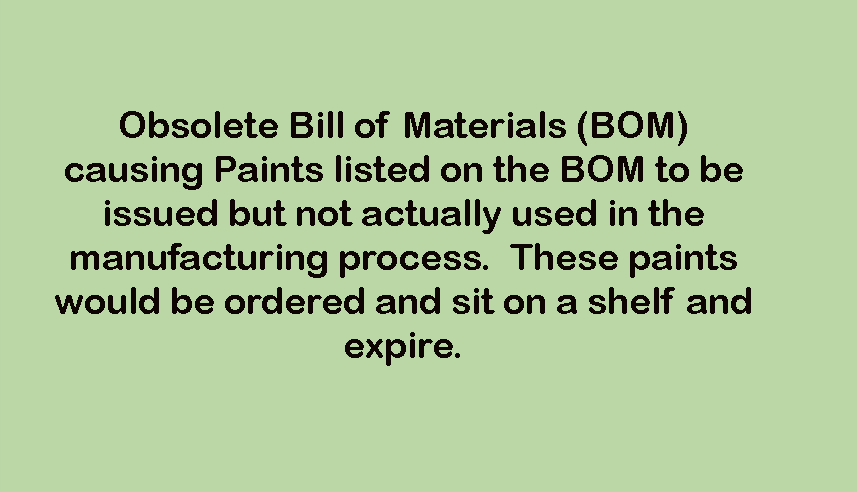
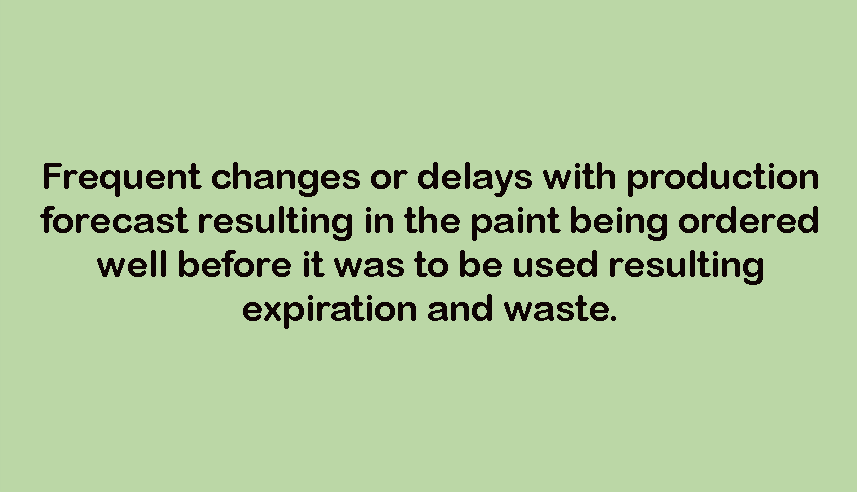
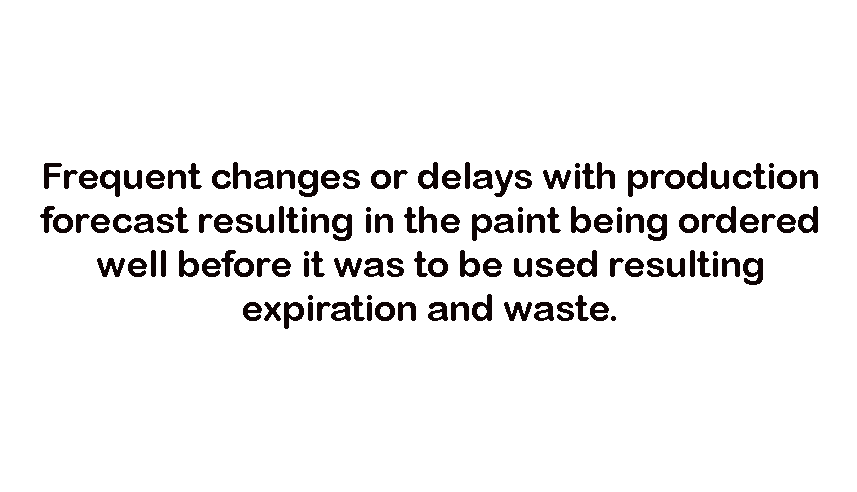
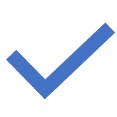
BOM Verification
Every individual paint was verified with each BOM to ensure it was required in the current production process. Those that were not required were removed from the BOM and inventory management plan
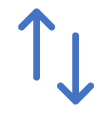
Minimum Order Reduction
Chemico was able to reduce the minimum order quantity through our supply chain. Our team also applied part grouping and sharing with other customer sites.
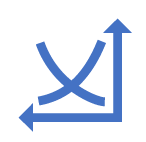
Demand Planning
Chemico established a formal communication with each department to verify product forecasts monthly to ensure inventory levels, forecasts, and pending orders were adjusted to optimize delivery and material shelf life.
Case studies
Project Results:
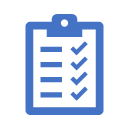
Improved product quality and flow-down compliance
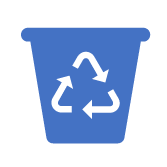
Reduction in annual paint consumption/ waste by 4,800+ gallons – 75% reduction
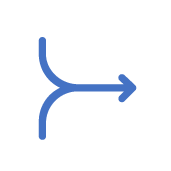
Product consolidation – Reduced number of Paints
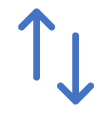
Optimized departmental communication
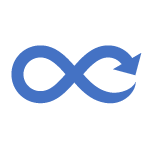